Understanding a lidar's specifications is crucial for grasping its capabilities and limitations in various applications. While terms like Maximum Detection Range may seem straightforward at first glance, nuances in measurement methods and target conditions can significantly impact their interpretation.
In this blog post we’ll delve into the complexities of lidar specifications, shedding light on what they truly signify and what crucial details they might not reveal.
Maximum Detection Range (Max Range):
ChatGPT may tell you that a lidar’s Maximum Detection Range is “typically defined as the maximum distance at which the lidar sensor can accurately detect objects or return signals”. But doesn’t “accurately detect objects” sound somewhat vague?
In fact, there is no industry-wide standard for how Max Range is exactly measured, and lidar companies can choose their own method based on common OEM requirements and product type.
For example, for one of our OEM customers, Max Range is measured at the longest distance at which the lidar can receive a certain number of points on a target of their specified size.
Other OEMs that we work with require a Max Range measured at the longest distance at which the lidar’s detection probability passes a certain percentage, mostly either 90% or 95%. Detection probability compares the number of a lidar’s actual returned points against its theoretical returned points. Normally, a lidar’s detection probability stays close to 100% from 0m to a certain distance; it starts to decrease drastically past that distance, and Max Range is where it drops to the minimum percentage required. The drop is so sharp that a 50% or 90% detection probability usually doesn't result in a big difference in the Max Range measured.
Despite the definition of detection probability based on an infinite-sized target, practical detection probability is affected by the geometry of the actual targets, which involves its shape, size and other boundary conditions. However, lidar companies don’t usually specify those things about the target they use when measuring and publishing Max Range.
Something that lidar companies do specify is the reflectivity of the target. Most commonly, you will see a marketed Max Range at “10% reflectivity”. Reflectivity refers to how well the surface of an object reflects light – the higher reflectivity, the more photons bounce back when hitting the object, thus the more points returned to the lidar. Reflectivity is dependent on the object’s material property and surface condition: for example, black tire < black car < white car. A black tire’s reflectivity is normally below 10%, and that’s why we use black tire detection to benchmark lidar performance:
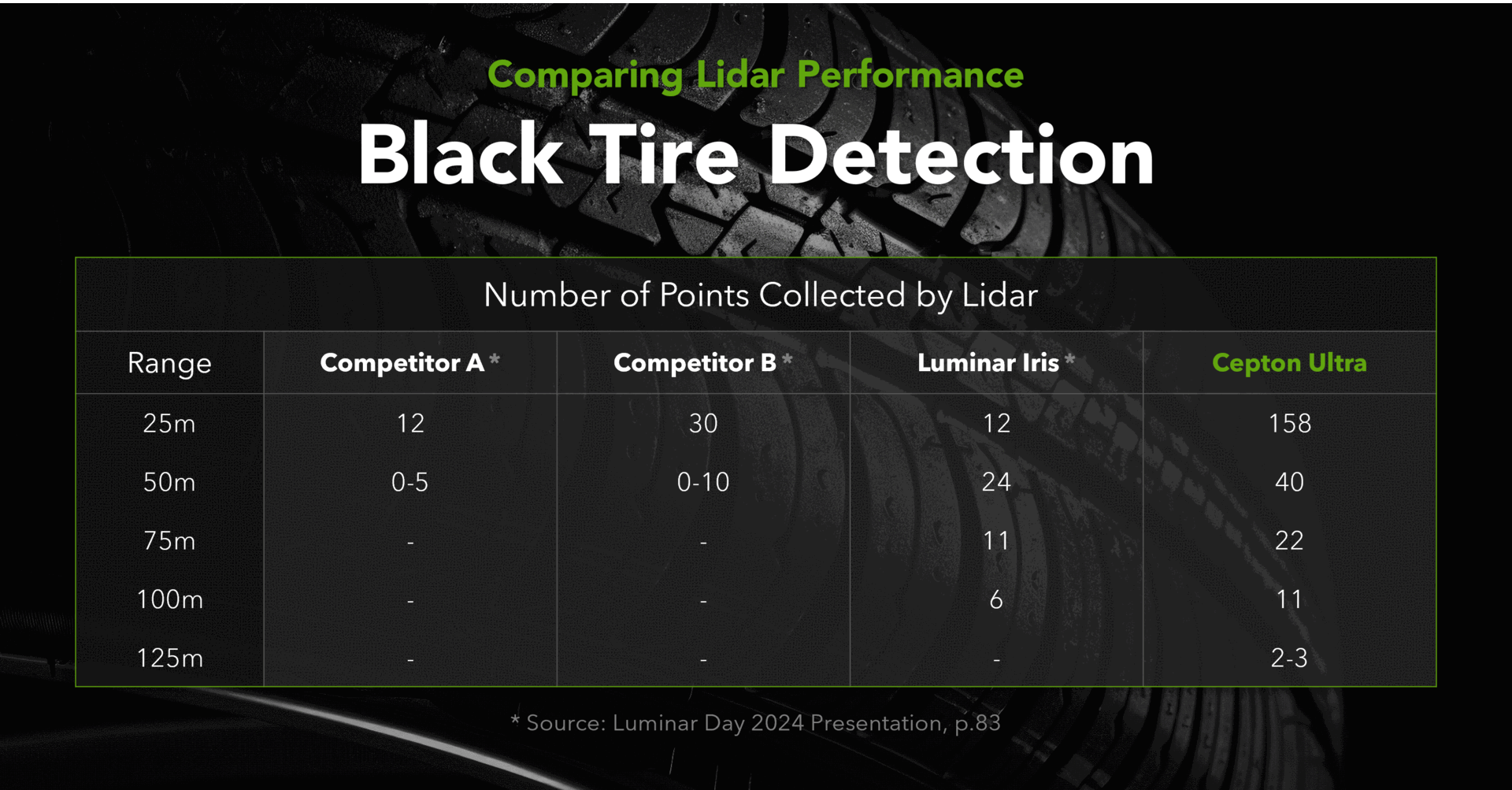
To learn more about what this comparison indicates, visit this blog post.
A lidar’s detection capability significantly decreases as the reflectivity declines. Roughly converted, a Max Range of 250m at 10% reflectivity represents the same detection capability of 500m at 40% or 750m at 90%. Therefore, reflectivity makes a huge difference and must be specified along with range.
Without knowing parameters such as target size, measurement method and required detection probability, it is hard to draw a 100% fair comparison between Maximum Detection Range numbers published by different lidar companies.
Despite those differences, naturally a 600m Maximum Detection Range at 10% reflectivity would still be more impressive than 250m at 10%. Now the question is: do lidars really need to achieve a 600m range for common automotive use cases? While “seeing” far is never a drawback, assisted and automated driving capabilities under current speed limits don’t require excessively long range – this blog post further explains why.
An excessively long range is not always something nice to have, as it often comes with a series of compromises in lidar field of view, footprint, power consumption and cost.
Field of View (FOV):
Simply put, Field of View is how big of a picture the lidar captures. Horizontal FOV and vertical FOV define the maximum angles within which the lidar is able to collect data. Naturally, the wider FOV, the bigger coverage of the lidar data, and one might think a 360° x 360° FOV would be the most potent solution.
The reality is: we’ve never seen a lidar that sends out light pulses in all directions, or shines like a disco ball (well, invisibly). There have been rotational lidars with a 360° horizontal FOV, which were the most common solutions during the early days of lidar’s adoption for autonomous driving applications.
However, rotational lidars have become significantly less favored by the automotive industry, as they offer highly limited integration options, break easily due to mechanical wear and tear and are very expensive. No mass-market consumer vehicle would want a spinning pod on its rooftop, and when embedded elsewhere in the vehicle, up to two thirds of the lidar’s horizontal FOV may become ineffective. The same would apply to most smart infrastructure use cases too – when mounted, nearly half of the light the rotational lidar sends out would hit the wall or be contained within the integrated system’s housing.
Therefore, effective FOV is what matters. We want every single point in the FOV to be useful, either detecting what’s out there or what’s not.
For most ADAS and autonomous driving applications, a 120° horizonal FOV would be sufficient for long-range lidar, as the OEMs are mostly concerned with hazards ahead of the vehicle across a few lanes. As for near-range lidar, it is used to monitor the vicinity of the vehicle, so its capability of seeing smaller objects closer to the ground is key. This would require a bigger vertical field of view. Our Nova lidar, with a 90° vertical FOV, is one of the most preferred near-range lidar solutions by OEMs around the globe, as it minimizes the gap between the ground and the sensor level, making it possible to accurately detect common objects within human and camera blind spots, such as small children, curbs and big rocks.
As OEMs have come to appreciate flexible lidar solutions, we at Cepton have also made our lidar FOV flexible. Our latest innovation, Ultra, offers maximum adaptability and versatility with software definable FOV. Depending on the use case, its field of view can be configured to be narrower or wider without any change to the hardware. This would make the lidar more adaptive across different driving scenarios to remain power efficient, depending on the number of lanes and the attention needed to roadside objects.
We have also incorporated software definable FOVs for regions of interest (ROI), where higher resolution is needed to collect more data on high-priority objects on the road, be it a car in front on the highway, or pedestrians in a busy local street. Here is a demonstration of how it’s done:
In a word, like many other specifications, don’t let high numbers intimidate you when it comes to lidar FOV. It is the effective FOV, FOV efficiency and suitability to specific OEM requirements and use cases that really matter. After all, cost, reliability and power efficiency are no less important than performance alone.
In our next blog post, we will discuss the interplay between key specifications such as Points per Second and Frame Rate, discuss how Angular Resolution and Range Accuracy reflect lidar performance, and why non-performance indicators like Power Consumption and Size are equally important for evaluating a lidar solution.